Projects
Six Cutting Process Comparison (1)
Preface
In modern manufacturing, although laser cutting equipment has become the first choice for most manufacturers. However, as traditional cutting equipment, it still holds a considerable market share in the market. Traditional cutting equipment mainly includes (CNC and non CNC) shearing machines, punching machines, flame cutting, plasma cutting, high-pressure water cutting, and other means. This article mainly discusses shearing machines, punching machines, and flame cutting processes.
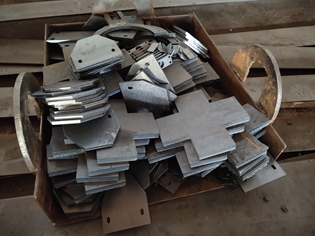
Introduction to Three Traditional Cutting Processes
First type: (CNC) shearing machine
Due to its main linear cutting method, although it can cut sheet metal up to 4 meters in one cut, it can only be used for sheet metal processing that only requires linear cutting. It is generally used in industries that only require linear cutting, such as cutting after flattening the board.
Second type: (CNC/turret) punching machine
There is more flexibility in curve machining. A punching machine can have one or more sets of square, circular or other special requirements of punches, which can process specific sheet metal workpieces at once. The most common is in the chassis and cabinet industry, where the required machining processes are mainly straight lines, square holes, circular holes, etc., with relatively simple and fixed patterns. They mainly face carbon steel plates below 2mm, with a width generally of 2.5m × 1.25m. Stainless steel with a thickness of 1.5mm or more usually does not use a punch due to the high viscosity of the material and the cost of the mold.
Its advantages are: fast processing speed for simple graphics and thin plate processing.
Compared to laser cutting equipment, the disadvantage of punching machines is their limited ability to press thick steel plates. Even if it can be punched, the surface of the workpiece will collapse, which incurs mold costs. The mold development cycle is long, the cost is high, and the degree of flexibility is not high enough. Cutting and processing of steel plates exceeding 2mm in foreign countries generally use more modern laser cutting instead of punching machines. Firstly, the surface quality of thick steel plates is not high during punching and shearing. Secondly, punching thick steel plates requires larger tonnage punching machines, which wastes resources. Thirdly, the noise during punching thick steel plates is too loud, which is not conducive to environmental protection.
Third type: flame cutting
As the initial traditional cutting method, due to its low investment and low requirements for processing quality in the past, adding another machining process when the requirements are too high can solve the problem, and the market retention is very large. Now it is mainly used to cut thick steel plates exceeding 40mm.
Compared to laser cutting equipment, the disadvantages of flame cutting are: excessive thermal deformation during cutting, too wide cutting seams, waste of materials, and slow processing speed, which is only suitable for rough processing.
Epilogue
These devices are not only well-known, but also affordable. Although they have obvious disadvantages compared to modern processes such as laser cutting, they each have their own unique advantages.