Projects
Six Cutting Process Comparison (2)
Preface
In modern manufacturing, laser cutting equipment has become the first choice for most manufacturers. However, as traditional cutting equipment, it still holds a considerable market share. The commonly used traditional cutting processes in the market now mainly include plasma cutting and high-pressure water cutting. This article mainly discusses laser cutting, plasma cutting, and high-pressure water cutting processes.
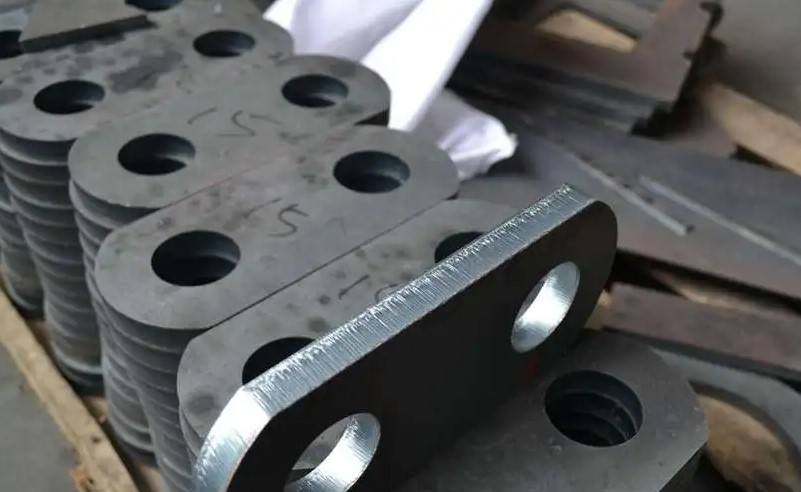
Introduction to Three Common Cutting Processes
Laser cutting
Laser cutting has a high degree of flexibility, fast cutting speed, high production efficiency, and short product production cycle, which has won a wide market for customers. Laser cutting has no cutting force and no deformation during processing; No tool wear, good material adaptability; Whether it is a simple or complex part, it can be precisely and rapidly formed and cut with laser in one go; Its narrow cutting seam, good cutting quality, high degree of automation, easy operation, low labor intensity, and no pollution; It can achieve automatic cutting layout and nesting, improve material utilization, lower production costs, and good economic benefits.
It should be noted that laser cutting machines require high acceleration cutting heads and motion platforms to ensure cutting accuracy. If the optical path or lens is affected by dust, grease, or other impurities, it will cause deviation in the cutting trajectory and reduce the cutting quality.
Plasma cutting&precision plasma cutting
Similar to flame cutting, the heat affected zone is too large, but the accuracy is much greater than flame cutting, and the speed has also made an order of magnitude leap, becoming the main force in medium plate processing. The actual cutting accuracy of top CNC precision plasma cutting machines has also reached the lower limit of laser cutting.
Compared to laser cutting technology, the disadvantage of plasma cutting is that the thermal deformation is too large and the slope is also large when cutting thin steel plates, making it powerless when high precision is required. During the cutting process, a large amount of dust is also generated, causing significant pollution to the environment. In addition, plasma cutting machines require a large amount of gas as necessary substances in processes such as arc and cutting, resulting in higher costs.
High pressure water cutting
It uses high-speed water jet mixed with diamond sand to cut sheet metal, with almost no material restrictions and a cutting thickness of almost 100mm or more. It can also cut materials that are prone to cracking during thermal cutting, such as ceramics and glass. Copper, aluminum, and other materials with high laser reflectivity can be cut with a water jet.
Compared to laser cutting technology, the disadvantages of high-pressure water cutting are: slow processing speed, not environmentally friendly, and low material utilization rate.
Epilogue
Overall, different cutting processes have their own advantages and disadvantages, and their scope of application also varies. If high precision, fine cutting lines, and no pollution are required, laser cutting equipment can be chosen.