Projects
Techniques For Optimizing Laser Cutting of Thick Plates
Stainless steel thick plate is a kind of material in many fields. The products it produces have excellent performance in all aspects and long service life. Now it is widely used in machinery manufacturing, construction engineering, kitchen ware manufacturing, rail vehicles and other industries. Nowadays, most stainless steel thick plates choose laser cutting, and to cut high-quality thick stainless steel plates, it is necessary to master certain skills.
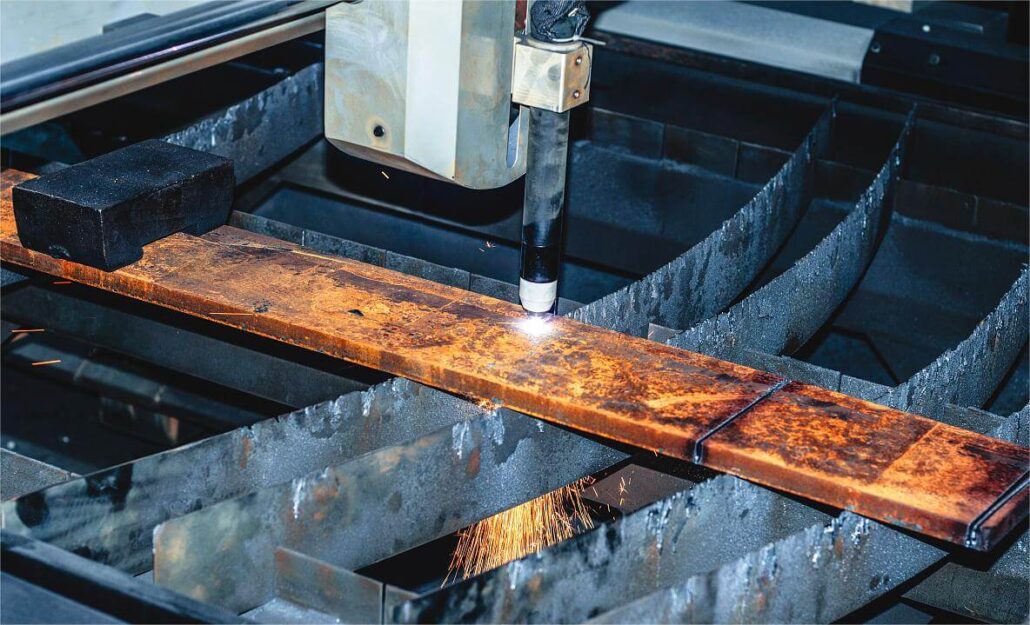
Selecting Nozzle Model
The diameter of the nozzle determines the shape of the airflow entering the incision, the gas diffusion area, and the gas flow rate, thereby affecting the removal of molten materials and the stability of laser cutting. The higher the air flow rate and speed entering the incision, and the appropriate position of the workpiece in the airflow, the stronger the ability of spraying to remove molten materials.
The thicker the stainless steel, the larger the nozzle should be, the larger the proportional valve setting, and the greater the flow rate to ensure pressure and achieve normal cross-sectional effect.
Coaxial Test
At the same time, to ensure the laser cutting effect and protect the nozzle from damage. Before cutting and processing, coaxial testing is also required to ensure that the nozzle is coaxial with the laser output beam.
The testing method is to apply transparent adhesive tape to the end face of the nozzle outlet, adjust the laser output power for drilling, observe whether there is a central hole and the position of the central hole on the transparent adhesive tape, and synchronously adjust the adjustment screw on the mirror cavity handle until the hole made by the laser on the transparent adhesive tape coincides with the center of the nozzle.
Debugging Frequency
The impact of frequency changes on the cutting of stainless steel thick plates: When the frequency decreases from 500-200Hz, the cutting section effect becomes finer, and the layering gradually improves. When the frequency is set to 100Hz, cutting cannot be carried out, and the best frequency range can be found through the change of frequency. To ensure the optimal cutting section, it is necessary to ensure a perfect match between the number of pulses and the energy of a single pulse.
Debugging Duty Cycle
The impact of duty cycle changes on the cutting of stainless steel thick plates: 53% duty cycle is the critical value, and further reducing the duty cycle results in incomplete cutting marks on the lower surface. The duty cycle increases to 60%, resulting in coarsening of the cross-section, obvious layering, and yellowing of the cutting surface.
Selecting Focus
The focal point is different, and the thickness, material, and quality that can be cut are also different. Cutting different materials and thicknesses requires adjusting to different focal points. Before cutting, measure the actual zero focal point to quickly determine the most suitable cutting point.