Projects
Why poor battery soldering quality
Factors Affecting The Welding Quality Of Battery Pack Modules Introduction
As research into laser welding technology continues to advance, significant strides have also been made in the fields of technology, process improvement, and defect remediation. Virtual welding frequently happens during the laser welding process of the PACK module, which negatively impacts the battery’s lifespan.
False welding occurs when there is insufficient or even no penetration between two (multi-layer) tabs or between the bus bar and the tab. The implications of this type of malfunction, which primarily impacts the battery’s electrical performance stability, are rather severe. The virtual welding of a solder joint frequently causes the entire battery pack to malfunction, and it is frequently an undetectable problem that becomes apparent after the client has used the product for a while.
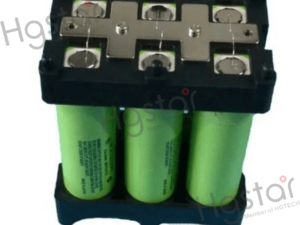
Lithium battery PACK modules require certain welding conditions for laser welding.
1. When assembling or welding, prevent short circuits.
2. During the welding process, the cell body’s influence on temperature should not be greater than 60 degrees Celsius.
3. The welding area’s minor oxidation area has no impact on the tabs’ conductivity.
4. Mass production can be automated.
5. There is a structure that combines multiple thin material tabs that have been welded together, and there may be welding between different materials like copper and aluminum.
6. When performing single-layer welding, the welding layer’s depth should be under control and impassible to welding.
Factors influencing the laser welding PACK module’s welding effect include:
1. Surface contamination of the substance
In general, be mindful of whether the material’s surface is dirty when utilizing a laser welding machine for welding. One of the elements that directly affects the instability of the laser welding machine is the surface of the material, which will not crystallize regularly or enough if dirt is introduced into the welding area.
2. Too much speed is used during welding
When utilizing a laser welding machine, users frequently believe in error that the higher the welding speed, the faster the production and the better the product. In actuality, the longer the processing time between the laser and the workpiece, the more sufficient the welding, not the faster the better; otherwise, the faster.
3. Incompatible welding power and materials
Not all materials are compatible with the strength of laser welding devices. Varying materials require different amounts of power to be welded. Low user power results in weak welds. For some highly reflecting materials, we can raise the welding power while reducing other welding process variables like welding speed.
4. Furniture and Tables
Materials are stored on tables and other furniture. For example, nanosecond laser welding equipment needs the two weldments to be thoroughly fitted in order to prevent false welding. If the material is not fixed securely enough, it may not be able to weld successfully, leading to poor welds and missing welds. Additionally, we must modify the fixture to accommodate challenging welding.